Some Ideas on Alcast Company You Should Know
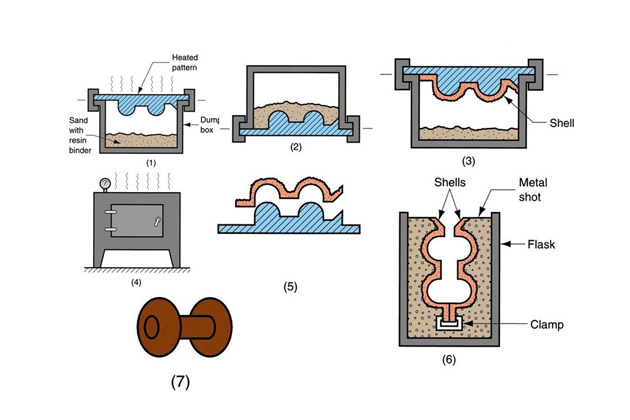
There are lots of small distinctions between functioned and cast aluminum alloys, such as that actors alloys can consist of much more considerable quantities of other metals than functioned alloys. But the most significant distinction between these alloys is the fabrication process where they will certainly go to provide the final item. Other than some surface area therapies, cast alloys will certainly leave their mold and mildew in nearly the precise solid type desired, whereas functioned alloys will undertake several adjustments while in their solid state.
If you assume that a functioned alloy might be the finest for your project, have a look at several of our short articles that describe more about specific functioned alloys, such as Alloy 6061 and Alloy 6063. On the various other hand, if you assume a cast alloy would be much better for you, you can find out more regarding some cast alloys in our Alloy 380 and Alloy 383 write-ups (coming quickly).
The Ultimate Guide To Alcast Company
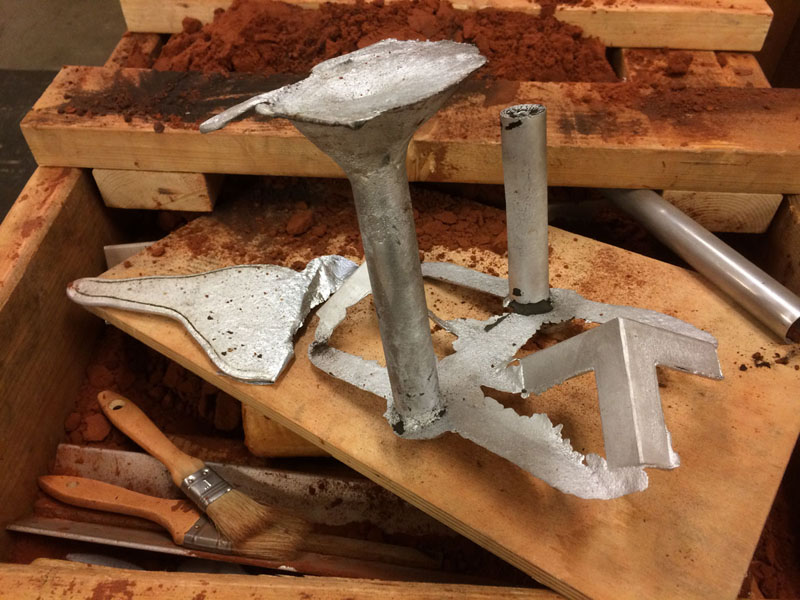
Having the experience and industry expertise to craft your spreadings for optimum production and quality outcomes will simplify the task. Making aluminum spreading calls for a complicated set of procedures to accomplish the appropriate results. When selecting a brand-new aluminum shop to companion with, guarantee they have comprehensive market experience and are educated about all elements of the aluminum spreading procedure: style, production, material evaluation, and item screening.
Some Known Facts About Alcast Company.
By selecting a business that offers services that meet or exceed your item needs, you can be sure that your project will certainly be finished with miraculous precision and effectiveness. Particular aluminum shops specialize in certain sorts of manufacturing procedures or casting techniques. Different parts require different manufacturing methods to cast light weight aluminum, such as sand spreading or die spreading.
Pass away casting is the name offered to the process of developing intricate metal parts with usage of mold and mildews of the component, also understood as dies. It produces more elements than any type of other procedure, with a high level of accuracy and repeatability. There are three sub-processes that fall under the classification of die casting: gravity die casting (or long-term mold casting), low-pressure die spreading and high-pressure die casting.
Despite the sub-process, the die spreading procedure can be damaged down into six steps. After the pureness of the alloy is tested, dies are developed. To prepare the needs spreading, it is essential that the passes away are clean, so that no residue from previous productions continue to be. After cleansing, the ejection lubrication is related to the die to make certain a smooth launch.
The pure metal, also called ingot, is included in the heating system and maintained at the molten temperature level of the steel, which is after that transferred to the shot chamber and infused into the die (aluminum casting manufacturer). The stress is then preserved as the metal strengthens. As soon as the steel strengthens, the cooling process starts
Alcast Company Things To Know Before You Get This
The thicker the wall of the component, the longer the cooling time due to the amount of interior steel that also needs to cool. After the part is fully cooled, the die cuts in half open and an ejection system pushes the component out. Following the ejection, the die is shut for the following shot cycle.
The flash is the additional material that is cast during the process. Deburring gets rid of the smaller items, called burrs, after the cutting procedure.
7 Simple Techniques For Alcast Company
Nevertheless, this proved to be an unreliable examination, since the tester can reduce into an item and miss out on a location with porosity. Today, leading manufacturers use x-ray screening to see the Visit Your URL entire interior of elements without cutting right into them. This enables them to more accurately accept or decline components. To obtain to the ended up item, there are 3 main alloys used as die casting product to choose from: zinc, aluminum and magnesium.
Zinc is one of the most used alloys for die casting due to its reduced price of raw materials (Casting Foundry). Its rust resistance also allows the components to be lengthy lasting, and it is one of the more castable alloys due to its reduced melting factor.
Alcast Company Can Be Fun For Anyone
As mentioned, this alloy is just one of the most typically utilized, yet produces will, sometimes, select aluminum over zinc due to light weight aluminum's manufacturing advantages. Aluminum is highly affordable and among the much more versatile alloys. Aluminum is made use of for a number of different products and sectors anything from window frameworks to aerospace materials.
Comments on “Not known Details About Alcast Company”